서 론
암반 구조물을 시공하기 위한 암반 굴착은 건설 초기에 수행하는 필수적인 절차이다. 국내에서는 암반의 강도와 절리 특성 등을 고려하여 기계 굴착과 발파 굴착으로 구분하여 굴착 방법을 결정하고 있다(KTX, 2003; KEC, 2012).
발파를 이용한 암반 굴착은 굴착 효율성 제고를 위해 대부분의 암반 굴착에 이용되고 있지만, 도심지 등 중요 구조물 근체에서 발파 작업을 수행할 때 인근 건물 및 구조물에 지대한 영향을 미칠 수 있으므로 발파 진동을 경감시키기 위한 다수의 발파 공법이 개발되었다. 그러나 발파 작업에 내재된 발파 특성은 발파 진동 및 발파 소음을 완전히 배제하기는 어려운 실정이다. 현재 발파에 의한 공해를 방지하기 위하여, 인장 강도가 압축 강도의 약 1/10배인 암석과 같은 취성 재료의 특성을 이용하여 팽창제, 가스압, 유압 등을 이용하여 암반을 파쇄하는 방법이 개발되어 있다. 이와 같이 발파를 배제한 방법은 무소음 및 무진동의 효과는 있지만 굴착의 효율성은 저하되어 국부적인 암반 절개 및 채석장 암석 블록 절단 등에 활용되고 있다.
최근 비발파 공법의 한계성을 극복하고 무소음과 무진동과 같은 장점을 지닌 수압암반절개기술을 개발하여 현장 적용성을 검토한 연구가 수행된 바 있다(Park and Lee, 2016; Park et al., 2017, 2019; Park and Woo, 2019). 수압암반절개기술은 그 동안 암반 내의 지중 응력 분포 특성을 파악하거나(Haimson, 1978; Haimson et al., 2003) 가스나 석유 등의 에너지자원 생산을 증진시키기 위해 사용하였던(Jung, 2011; Cheon and Lee, 2013) 수압파쇄방법을 암반 절개에 응용한 것으로 시추공에 높은 유량과 고압을 재하하여 암반의 절개 방향을 제어하기 위해 개발되었다. 따라서 이 방법은 기존의 발파에 의한 굴착과는 달리 무진동 및 무소음의 장점이 있다.
본 연구는 수압암반절개 시스템의 굴착 효율성을 개선하기 위해 이중 패커 및 유량공급장치를 개량하였으며, 현장 굴착에 적용하여 굴착 효율성을 판단하였다.
개선된 수압암반절개시스템
수압암반절개를 위한 시스템의 가장 핵심적인 장치는 고압 및 대유량을 공급할 수 있는 수압공급장치와 시추공에 삽입되어 압력과 유량의 손실없이 암반에 인장력을 가할 수 있는 패커이다. 본 연구에서는 굴착 효율을 증대시키기 위하여 이전의 시스템(Park and Woo, 2019)에서 사용하였던 고압 패커 및 수압공급장치를 개량하였다.
기존의 이중 고압 패커(Park et al., 2017)는 시추공벽에 밀착하기 위하여 패커 외곽을 둘러싼 고무는 고압에도 견딜 수 있는 재질을 사용하였으며, 고압의 물에 의해 패커를 팽창시키는 방법을 사용하였다. 기존의 패커는 고압의 물에 의해 팽창된 외곽의 고무가 시추공벽에 밀착되기 때문에, 직접적인 수압의 영향 이외에도 패커 또한 시추공벽에 큰 인장력을 가하여 굴착에 용이한 점도 있었지만, 패커 고무 재질의 한계로 인하여 지속적으로 여러 번 사용할 수는 없는 제약이 있었다. 이러한 제약을 극복하기 위해 본 연구에서 개발한 쐐기형 고압 이중패커는 30 MPa의 고압에서도 시추공 내에 가해진 수압과 유량이 유실되지 않고 여러 번 사용할 수 있도록 우레탄과 팽창성 고무를 사용하여 성능을 개량하였다(Fig. 1).
기존의 패커가 수압으로 팽창된 패커 외부의 고무가 시추공벽에 밀착되지만, 쐐기형 고압 이중패커는 패커 내부에 장착된 유압 피스톤에 의해 쐐기 형태의 실린더가 전진하여 우레탄 및 팽창성 고무를 시추공벽에 밀착시키는 원리를 이용한다. 기존의 패커에 사용되었던 고무는 거친 시추공벽에 고압으로 밀착되면 고무에 손상에 발생하기 때문에, 재활용이 어려운 경우가 종종 발생하여 고무를 교체하여야 하는 번거로움과 비용이 발생하였다. 또한 고압으로 팽창된 패커는 압력 제거 이후에도 원상으로 수축되는데 시간이 다소 소요되거나, 완전히 원상으로 수축되지 않는 경우도 발생하였다. 쐐기형 고압 이중패커는 유압으로 작동하기 때문에 패커 압력 증가와 감소 제어를 용이하게 조절할 수 있고, 시추공벽과 밀착되는 부분은 우레탄과 팽창성 고무로 이루어진 부분이므로 손상이 적게 발생한다. 또한, 필요시 우레탄 부분만 교체하면 재사용이 가능하므로 보다 경제적이다.
수압에 의해 유도된 균열은 대부분 미세 균열로 암반 절개에 충분한 절리 틈새를 형성시키지 못하기 때문에, 실질적인 암반 굴착이 발생되기 위해서 시추공 내에서 충분한 인장 변위를 발생시킬 수 있어야 한다. 따라서 본 실험에서는 수압파쇄균열이 발생한 후 이중 고압 패커를 제거하고, 고압의 물을 주입하여 팽창시킨 단일 패커(Fig. 2)를 사용하여 암반 절개를 위한 변위를 발생시켰다.
Park and Woo(2019)는 유량 50 L/min 수압 50 MPa의 성능의 수압공급장치를 이용하여 수압균열 유도에 따른 암반 파쇄를 발생시켰지만, 수압균열 확장이 제한적이었기 때문에 굴착 범위도 시추공 주변부로 국한되었다. 따라서 본 연구에서는 수압균열 확장을 연장시키기위하여 최대 유량 300 L/min, 최대 수압 30 MPa으로 물을 주입할 수 있는 4-channel 수압공급장치를 제작하였다(Fig. 3).
현장 실험
개량된 수압절개시스템의 굴착 성능은 충청남도 보은군에 위치한 채석장에서 현장 굴착 실험을 통하여 평가하였다. 현장 실험 위치는 중생대 쥬라기의 흑운모 화강암과 화강섬록암으로 이루어진 보은화강암이 기반암으로 분포하는 지역이다(Fig. 4).
현장 실험은 연구지역의 흑운모 화강암 암반에 대하여 수행하였으며, 실험 지역의 화강암에는 4개의 절리군이 주로 분포한다. 즉, 평탄하고 운모류가 피복된 주절리군인 N80°E/60°SE과 이를 교차하는 N10°E/80°SE, N10°E/30°NW 및 N40°W/70°SW 등과 같은 절리군이 주요 절리군을 구성하고 있다(Fig. 5a). 실험 대상 암반을 지상 Lidar로 스캔하여 획득한 점군데이터(Fig. 5b)를 이용하여 실험대상 암반의 높이 6 m, 주절리군인 N80°E/60°SE 절리군의 간격이 평균 2 m인 것으로 분석되었다.
현장 수압암반절개실험은 Fig. 6과 같이 주절리군인 N80°E/60°SE을 따라 형성된 암반 사면에서 수행하였다. Fig. 6과 같이 A1, A2, A3 구역에서 을 수행하였고, 시추공은 수평 방향이며 각 시추공 사이의 간격은 0.5 m로 시공하였다. 시추공 지름은 109 mm, 연장은 1.8 m로 모든 시추공에 대하여 동일하다. 각 실험에서 모든 시추공에 물을 주입하여 균열 발생 및 누수 등을 관찰하였으며, 데이터로거를 이용하여 공내 압력변화를 실시간으로 측정하였다.
실험
A1 구간
Fig. 7과 같이, A1 구간에는 3개의 수평 시추공 A1-1, A1-2, A1-3을 우측 자유면과 평행하게 수직으로 설치하고 A1-2, A1-3, A1-1 시추공에 순차적으로 10초 간격으로 300 L/min의 유량으로 주입하면서 나타나는 압력 변화를 측정하였다(Fig. 8).
최초 주입공인 중앙에 위치한 A1-2공의 주입압은 3.5 MPa의 최대 압력을 보이고 있으며, 두 번째 주입공인 최상부공 A1-1공에서는 최대 압력이 나타나지 않으나 약 2 MPa 정도의 주입압이 유지되며, 마지막 주입공인 A1-3에서는 A1-1보다 높은 주입압이 유지되었다. Fig. 7과 Fig. 9에 보이는 수압파쇄균열은 사면 오른쪽에 형성된 자유면과 평행한 균열이 A1-2공과 A1-3공 사이에서 시작되면서 사면 전체로 균열이 전파되었다. 주입 후 A1-2와 A1-3공의 내부에는 각각 0.8 m와 1.0 m 깊이에서 주응력면으로 작용하고 있는 자유면과 평행한 수압파쇄균열이 형성되었다. 주절리군과 교차하는 A1-1공은 다른 시추공과는 달리 내부에 수압파쇄균열이 발생되지 않았으며, Fig. 7에 나타난 것과 같이 주입수 대부분이 사면 뒷편의 절리를 따라 누수되면서 더 이상의 균열 전파는 발생하지 않았다.
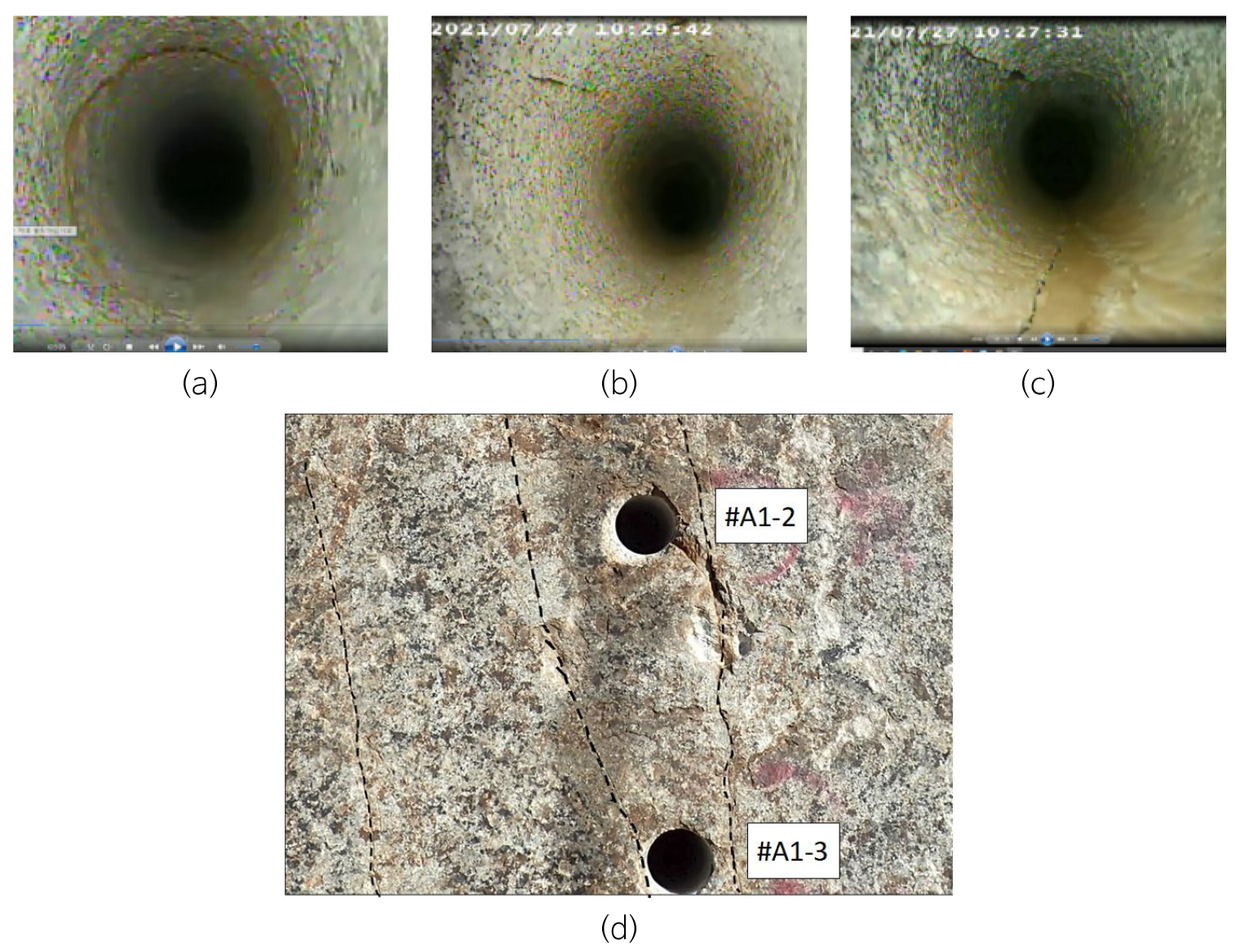
Fig. 9.
(a) Inside of borehole A1-1 with only one pre-existing fracture (N80°E/60°SE parallel with slope surface) and fractures induced by injection testing. (b) Borehole A1-2 at a depth of 0.8 m. (c) Borebole A1-3 at a depth of 1.0 m. (d) Vertically induced hydraulic fracutres on the surface around boreholes A1-2 and A1-3.
A2 구간
Fig. 10과 같이, A2 구간에서는 마름모형으로 배열된 4개의 시추공에 대하여 A2-1, A2-3, A2-2, A2-4 순서로 순차적으로 주입하였다.
기존 절리를 관통하는 A2-2공을 제외하고는 모든 주입공에서 3.8~4.5 MPa의 최대 압력이 나타났다. A2-1공에 주입한 후 암반 표면에는 A2-1공과 교차하는 수직절리를 따라 누수가 발생하였으며(Fig. 10b), A2-1공 내부에 새로운 수압파쇄균열은 형성되지 않았다. 즉, Fig. 11에 나타난 A2-1공의 주입압의 최댓값은 기존 절리가 개구된 압력값으로 판단된다. A2-3공 주입 후 0.5~0.8 m구간에서 수직의 수압파쇄균열이 발생하였고(Fig. 10d), A2-4공 주입 후에는 0.3~0.8 m 구간에서 새로운 수직 수압파쇄균열이 발생하였다(Fig. 10e).
반면 Fig. 10c에 나타난 것과 같이, A2-2공을 관통하는 주절리군과 이와 연결된 수직절리군을 따라 대부분의 주입수가 누수되어 다른 주입공에 비하여 낮은 주입압을 나타내고 있다(Fig. 11). 또한 주입에 의하여 주입공 내부에서 새롭게 형성된 수압파쇄균열은 암반 표면까지 연장되지 않았으나 기존 수직절리군의 틈새가 주입으로 더욱 확장되어 있었다.
A3 구간
Fig. 12와 같이, A3 구간에서도 마름모형으로 배열된 4개의 시추공에 대하여 A3-1, A3-2, A3-4, A3-3 순서로 순차적으로 주입하였으며, Fig. 12b~12d와 같이 수압파쇄균열 발생 및 Fig. 13과 같이 압력 변화를 파악하였다. A3 구간에서는 A3-1공에서는 수평절리가 주입 구간에 미세하게 발달하였으며(Fig. 12b), A3-2공과 A3-4공 주입 구간에서 수직으로 생성된 균열이 약 30°의 경사를 지닌 수압파쇄균열로 시추공 입구까지 연장되어 있다(Fig. 12c, 12e). Fig. 13이 나타내는 것과 같이, 기존 균열로 누수가 발생한 A3-3공에서는 첨두 압력값이 나타나지 않으며 A3-2와 A3-4공에서는 각각 1.7 MPa, 2.1 MPa의 최댓값을 보이고, A3-1공에서는 3.1 MPa의 최댓값을 나타낸다. 주입에 의하여 A3-4공의 수압파쇄균열과 연결된 경사 균열이 암반 표면에 형성되었다.
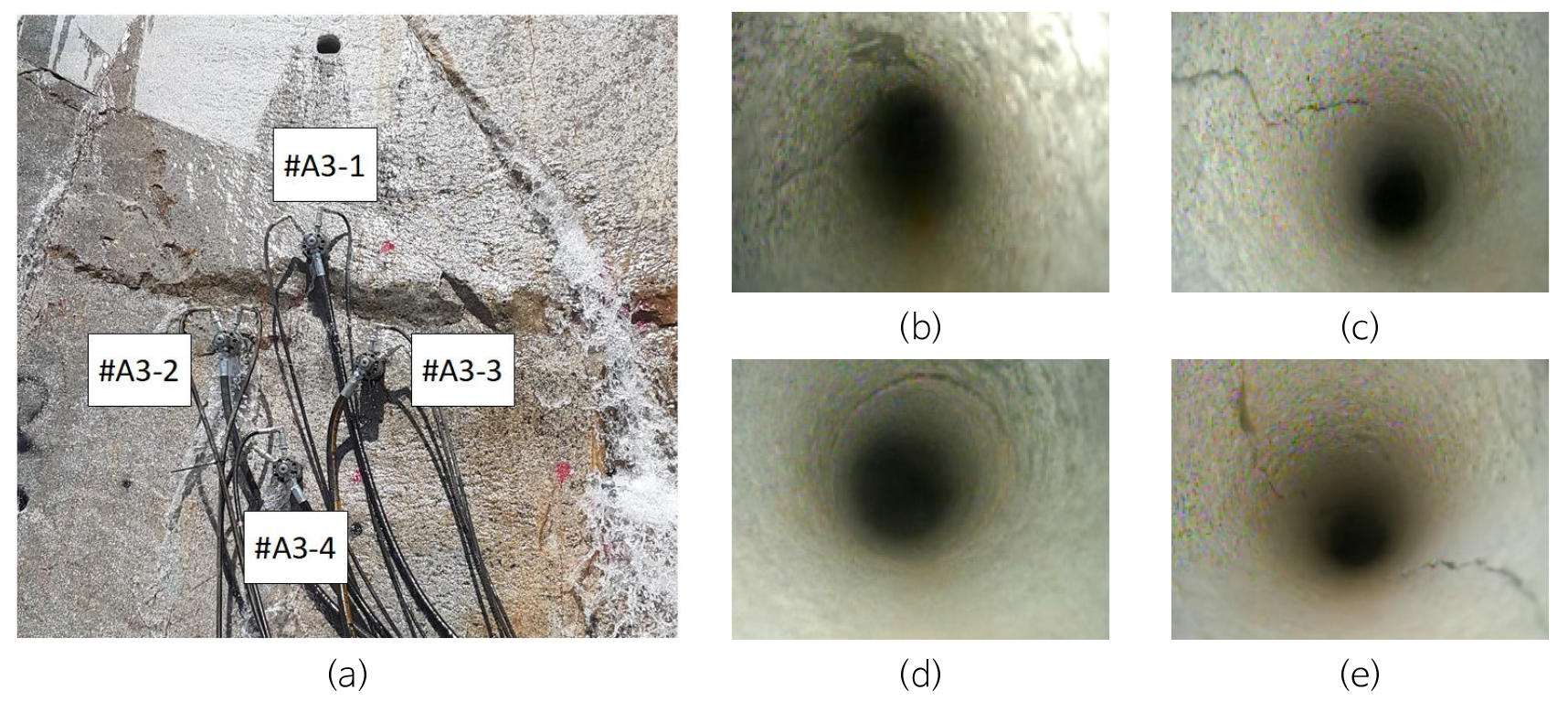
Fig. 12.
(a) Injection tests for four boreholes in ah rhombus array in section A3. (b) Horizontal hydraulic fracture inside borehole A3-1. (c) Inclined fracture at the entrance of borehole A3-2 prolonged by vertical hydaulic fracture in the injection interval. (d) Pre-existing main joint set in borehole A3-3. (e) Inclined hydraulic fracture at the entrance of borehole A3-4 prolonged by vertical hydaulic fracture in the injection interval.
패커 팽창 실험
실험에서 유도된 수압파쇄균열은 1~3 mm 정도의 틈새를 지니고 있으나 암반 굴착에 충분하지 않기 때문에, 암반 굴착을 위해서는 수압파쇄균열에 충분한 인장 균열을 유발하여야 한다. 이를 위하여 본 실험에서는 A1 구간과 A3 구간에 대하여 Fig. 2의 단일 패커를 시추공에 설치한 후 패커를 팽창시켜 인장 균열을 유발하는 암반절개실험을 수행하였다(Fig, 14, Fig. 15).
A1구간에 대해서는, 자유면 근처의 3개의 주입공 중 Fig. 8에서처럼 주입압이 최댓값을 보인 A1-2공에 대하여 단일 패커를 설치하였다. 단일 패커를 고압의 주입수로 팽창시키면서 발생하는 인장력을 이용하여 수압파쇄균열의 인장 변위를 발생시킨 결과, Fig. 14a에서와 같이 자유면과 평행한 방향으로 암반절개가 발생하였다. Fig. 14b에 나타난 것과 같이 단일 패커의 최대 압력인 17.4 MPa에 도달하였을 때, 주입으로 형성된 수압파쇄균열이 상부의 기존 절리와 연결되면서 절개가 발생하였으며, 패커의 팽창 범위까지 인장 균열의 틈새가 확장되었다. 실험에서 A1-2공의 최대 주입압은 약 3.5 MPa이었지만, 패커 팽창 실험에서 기록된 최대 패커 압력은 최대 주입압보다 약 5배 높은 17.3 MPa이었다.
A3 구간에서는 A3-2공에 대하여 패커 팽창 실험을 수행하여 실험에서 형성된 수압파쇄균열에 대한 인장 변위를 발생시켰다. Fig. 13에 기록된 A3-2공에 대한 실험에서의 최대 주입압은 1.7 MPa이며, Fig. 15b에서와 같이 패커 팽창 실험에서 기록된 최대 패커압은 10.9 MPa로 최대 주입압보다 약 6배 이상 높은 압력값을 나타내고 있다.
수치해석 결과와의 비교 분석
A1 구간과 A3 구간에서 수행한 실험과 패커 팽창실험 결과를 분석하기 위하여 FLAC2d(Itasca, 2016)을 이용하여 시추공 주입 및 패커 팽창실험에 따른 주변 응력의 변화를 분석하였다.
A1 구간을 모사하기 위하여 A1 구간에 적합한 수치모형을 설정하였다. 즉, 6 m의 암반이 상재 하중으로 작용하는 0.25 m × 0.25 m 크기의 모델 내부에 3개의 수직 주입공을 배열하였다. 모델의 오른쪽 경계는 A1 구간에서와 같이 자유면으로 구속없이 설정하였으며, 왼쪽 경계와 하부 경계는 수평 변위는 허용하고 수직 변위는 허용하지 않는 경계로 설정하였다. 실제 실험에서 관측한 각 주입공의 최대 압력을 고려하여 A1-1, A1-2, A1-3공에 대하여 각각 2.0 MPa, 3.5 MPa, 2.0 MPa을 적용시켰다(Fig. 16a). Fig. 16a와 같이, 인장응력이 작용하는 영역은 A1-2과 A1-3 중앙 위쪽 영역과 A1-3공 주변부이며, 중앙에 위치한 A1-2공 상하부에 5.5 MPa의 최대 인장응력이 형성된다. 암반에 기존에 분포했던 절리 또는 암반의 인장 강도에 따라 인장응력이 작용하는 영역에서 A1 구간 결과처럼 인장 절리가 형성될 수 있다. 즉, Fig. 16a는 주입공 간의 인장 영역이 연결될 만큼의 충분한 주입압력이 형성되지 않아 주입공 주변으로만 국부적인 인장 절리가 형성될 수 있음을 제시하는 수치해석 결과이다. 현장 실험에서는 주입한 물이 주입공 및 그 주변에서 새롭게 형성된 수압파쇄균열을 따라 누수되었기 때문에 더 이상의 주입 압력 증가는 발생하지 않았다. Fig. 16b는 A1-2공에 대하여 10.0 MPa의 패커 압력을 적용한 패커 팽창 결과 나타나는 최소주응력 분포를 보여준다. A1-2공 주변에 가장 큰 인장응력이 작용하고 있으며, A1-2공과 A1-3공 사이에 나타나는 인장 영역 경계는 Fig. 14a의 패커 팽창으로 인한 균열과 유사함을 볼 수 있다.
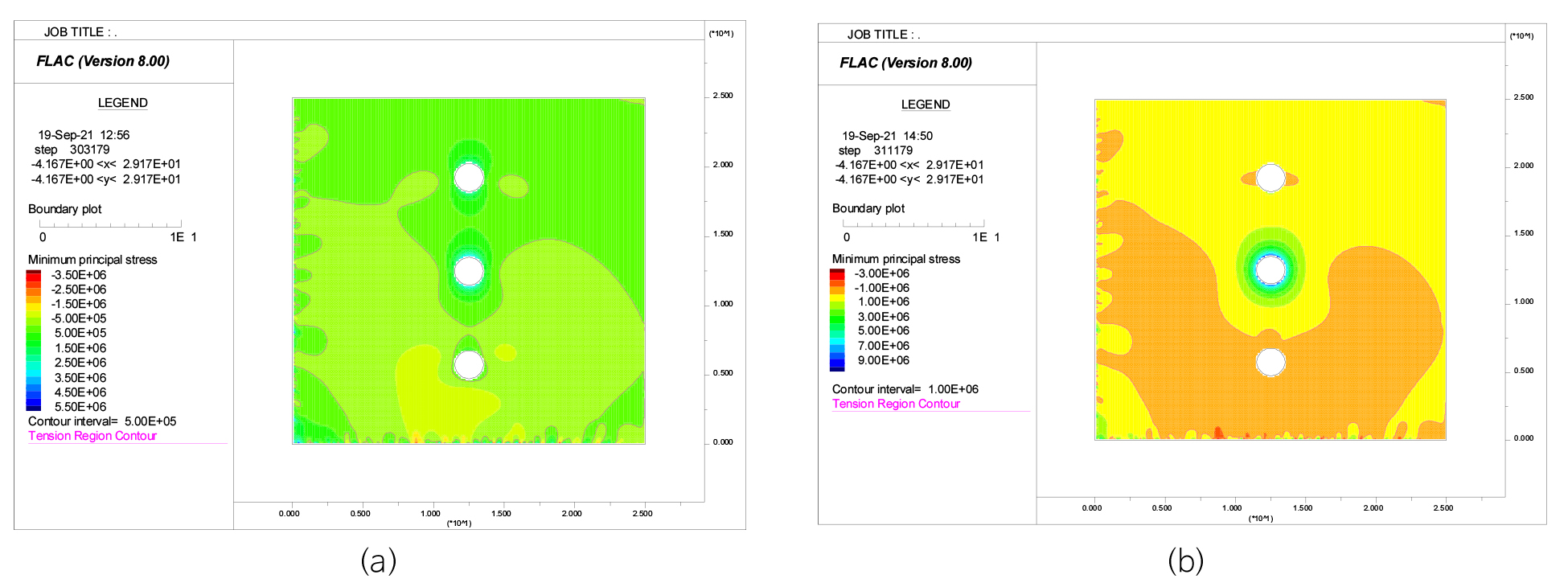
Fig. 16.
Minimum principal stress distribution around injection holes in section A1 modeled by FLAC2d using injecti0on pressure of (a) 2.0 MPa for borehole A1-1, 3.5 MPa for borehole A1-2 and 2.0 MPa for borehle A1-3. (b) Simulation of packer inflation test with 10 MPa packer pressure for borehole A1-2.
A3 구간에 대한 수치모형은 A1 구간의 모형과 마찬가지로 0.25 m × 0.25 m 크기의 모델 내부에 4개의 주입공을 마름모형으로 배열시켰으며, A3-3공 오른쪽에 위치한 절리면을 자유면으로 고려하였고 왼쪽과 하부 경계는 수직 및 수평 변위를 제한한 경계조건을 부였다. 현장 에서 측정한 결과를 바탕으로 A3 구간에 4개의 공에 대하여 2.0 MPa의 주입압이 적용하여 해석을 수행하였다(Fig. 17a). 상부공과 하부공인 A3-1과 A3-4공의 상부와 하부에 최대 인장응력이 형성되고, A3-2공은 A3-1공을 향하여 약 45° 기울어진 방향으로 인장응력이 형성되며, 자유면과 가까운 A3-3공은 주입공 상부와 하부에 최대 인장응력이 형성되어 있다. 또한 4개의 주입공 주변에서 나타난 인장 영역 구간이 모두 연결되어 나타난다. 현장 에서 주입수의 누수로 인하여 주입공 내의 압력이 2.0 MPa 정도로 제한되었기 때문에, Fig. 17a는 수압파쇄균열이 1.0 MPa 이하의 인장응력에서 형성되었음을 보여주고 있다. Fig. 17b는 A3-2공에 대하여 10.0 MPa의 패커 압력을 적용한 패커 팽창에서 나타난 최소주응력분포를 보여준다. 패커 압력 증가로 인하여 형성된 A3-2공 주위의 인장응력은 암반 전체를 자유면 방향의 변위를 발생시킨다. 이러한 수치해석 결과와 현장에서 수행한 패커 팽창 결과인 Fig. 15a를 서로 비교하면 인장 영역에서 균열이 확장 또는 생성되었음을 볼 수 있다. 즉, Fig. 15a에서의 A3-2공 하부에 나타난 경사진 암반 균열의 변위는 패커 팽창에 의한 인장 영역 범위 내에서 발생하였고, A3-1공과 A3-3공 상부에 형성된 인장 영역에서도 인장 균열의 발생 또는 확장이 형성되었음을 보여준다.
토의 및 결론
본 연구에서는 수압암반절개시스템을 개량하여 기존의 시스템이 가졌던 굴착의 효율성을 증대시키고자 하였다. 이를 위하여 패커 시스템과 주입 시스템을 개선하였으며, 암반 굴착에 필요한 변위를 제공하는 단일 패커를 도입하였다.
개선된 수압암반절개시스템을 이용하여 충청남도 보은지역에 분포하는 흑운모 화강암반에 대하여 3개의 구간-A1, A2, A3-으로 구분하여 수압암반절개실험을 수행하여 굴착 효율성을 분석하였다. 굴착 효율성 분석을 위하여 주입공의 압력 변화를 측정하고, 실험 전후의 암반 상태를 비교하여 균열의 생성 및 확장을 관찰하였으며, 이 결과를 바탕으로 FLAC2d을 이용한 수치해석을 수행하여 현장 실험 결과와 비교하였다.
현장에서 수행한 실험에서는 주입공과 교차하는 절리 및 생성된 수압파쇄균열이 기존 절리와 교차하면서 발생하는 누수로 인하여 주입압의 손실이 발생할 수 있다. 이로 인하여 수압파쇄균열의 확장 및 연장이 제한되어 현장 실험에서 암반 굴착에 충분한 변위를 얻을 수 없었다. 현장 실험에서 유도된 수압파쇄균열은 2~4 MPa 정도의 낮은 주입압에서 형성되어 균열의 확장 및 연장이 제한적이었다. 본 연구에서는 수압파쇄균열의 확장 및 연장을 위하여 주입공 내부에 설치된 단일 패커의 팽창력을 이용하였다. 수압파쇄균열 발생 압력보다 5~6배 높은 팽창력에 의한 인장응력과 이에 따른 인장 변위는 이미 생성된 수압파쇄균열의 변위를 확장시켜 암반 굴착을 용이하게 하였다.
현장 실험 결과를 바탕으로 수행한 수치해석결과에서는 수압파쇄균열 발생 압력에서는 국부적인 균열이 생성되며, 패커 팽창실험에 적용한 패커 압력에서는 해당 암반에 대하여 전반적으로 인장응력이 형성되어 균열의 확장 및 변위가 발생할 수 있다는 것으로 보여주고 있다.